The PSPO Advanced training was highly engaging and really changed how I look at product ownership. It broke the static v...
Table of Contents
-
What is Rapid Prototyping?
-
The History of Rapid Prototyping
-
How Does the Rapid Prototyping Process Work?
-
Why is Rapid Prototyping Important in Manufacturing?
-
Advantages of Rapid Prototyping
-
Main Techniques Used in Rapid Prototyping
-
Conclusion
Rapid prototyping is a game-changer in modern engineering and manufacturing, driving innovation and speeding up the product development process. This article explores the essence of rapid prototyping, its historical evolution, and the various techniques and tools used in the field.
What is Rapid Prototyping?
Rapid Prototyping (RP) refers to a suite of techniques used to quickly create a scale model or a part from three-dimensional computer-aided design (CAD) data. It emerged in the late 1980s as a revolutionary method aimed at accelerating product development. The core idea behind rapid prototyping is to swiftly translate digital designs into physical objects, facilitating faster iterations and improvements.
The History of Rapid Prototyping
The story of rapid prototyping is as fascinating as its applications. It all began with Chuck Hull, who, in 1984, invented the first 3D printer and introduced the world to stereolithography (SLA). This groundbreaking technology used a laser to cure photosensitive resin, creating three-dimensional objects layer by layer.
Since Hull's invention, rapid prototyping has evolved significantly. Early methods like SLA paved the way for newer technologies such as Fused Deposition Modeling (FDM) and Selective Laser Sintering (SLS). These advancements have expanded the range of materials and applications, making rapid prototyping a crucial tool in industries from aerospace to healthcare.
How Does the Rapid Prototyping Process Work?
Understanding the rapid prototyping process sheds light on its impact on manufacturing and product development. Here’s a step-by-step breakdown:
-
Design Creation: A digital 3D model of the object is created using CAD software. This step lays the groundwork for the prototype.
-
Data Preparation: The CAD model is converted into a format compatible with the chosen rapid prototyping technology, usually an STL file.
-
Machine Setup: The prototyping machine is prepared, calibrated, and loaded with the appropriate materials, such as plastic, resin, or metal powders.
-
Prototype Building: The machine constructs the prototype layer by layer according to the CAD specifications.
-
Post-Processing: After building, the prototype may need additional work, such as sanding, painting, or assembling, to achieve the desired finish.
Become an Expert in Product Ownership Stances with Professional Scrum Product Owner™ – Advanced (PSPO-A) Training
Expand your Product Owner skills with advanced techniques and strategies in PSPO-A training. Elevate your role in product delivery and stakeholder management.
Enroll Now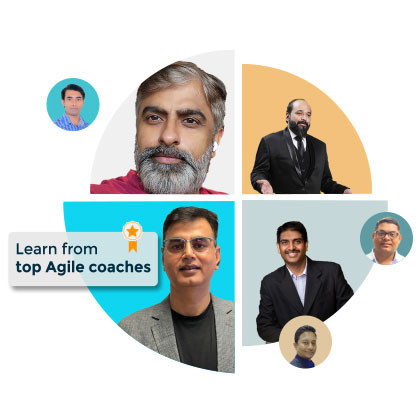
Why is Rapid Prototyping Important in Manufacturing?
Rapid prototyping holds significant importance in manufacturing due to its ability to quickly produce physical objects from digital designs. The benefits are manifold:
-
Speed: Rapid prototyping accelerates the design and development process, allowing for quicker responses to user feedback and market demands.
-
Cost-Efficiency: By detecting design flaws early, it helps avoid expensive revisions and tooling changes during mass production.
-
Design Quality: The ability to create and test multiple prototypes improves the final product's quality.
-
Iterative Design: It facilitates multiple iterations, helping development teams identify and address issues early on.
-
Functional Testing: Prototypes can be used to test functionality and usability before full-scale production, ensuring a higher-quality final product.
Advantages of Rapid Prototyping
Rapid prototyping offers several advantages that make it a preferred choice in various industries:
1. Speed of Development
One of the most notable benefits of rapid prototyping is its ability to quickly transform concepts into working models. This speed accelerates the design iteration process, allowing teams to rapidly respond to user feedback and market demands. By reducing the time required to develop prototypes, businesses can stay agile and competitive in an ever-evolving market.
2. Cost Reduction
Rapid prototyping plays a significant role in reducing development costs. By identifying and addressing design flaws early in the process, it helps prevent expensive revisions and tooling changes during mass production. Early detection of issues not only saves money but also helps streamline the overall development process, leading to cost-effective outcomes.
3. Improved Design Quality
The iterative nature of rapid prototyping leads to a more refined final product. With the ability to create and test multiple prototypes quickly, designers can make necessary improvements to both design and functionality. This iterative approach ensures a higher quality end product that better meets user needs and market expectations.
4. Enhanced Creativity and Innovation
Rapid prototyping encourages experimentation and innovation by allowing designers and engineers to explore a variety of options and solutions. Without the constraints of traditional prototyping methods, which can be time-consuming and costly, teams are free to push the boundaries of creativity and explore new ideas.
5. Customization and Personalization
The flexibility of rapid prototyping makes it ideal for customization and personalization. This is especially beneficial in industries like medical devices and consumer products, where individual needs and preferences are crucial. The ability to quickly produce customized prototypes ensures that designs can be tailored to meet specific requirements.
6. Functional Testing
Prototypes created through rapid prototyping are often robust enough for functional testing. This capability provides valuable insights into a product's performance and usability before it enters full-scale production. Thorough functional testing helps ensure that the final product is reliable and effective.
7. Material Diversity
Rapid prototyping techniques accommodate a wide range of materials, from plastics to metals. This material diversity allows for the testing of products under realistic conditions and material properties. It enables teams to evaluate how different materials affect the performance and durability of their prototypes.
8. Stakeholder Engagement
Physical prototypes facilitate more effective communication and decision-making with stakeholders. Having a tangible product to assess helps in gaining valuable feedback and aligning expectations. This engagement is crucial for refining the design and ensuring that all parties involved are on the same page.
9. Reduction in Waste
Many rapid prototyping methods, such as additive manufacturing, are more material-efficient compared to traditional manufacturing techniques. By minimizing material waste, these processes contribute to more sustainable production practices and reduce environmental impact.
10. Market Advantage
The ability to develop products rapidly provides a competitive edge in the market. Companies that can quickly iterate and bring new products to market often have a significant advantage over their competitors. Rapid prototyping helps businesses stay ahead by enabling faster development and deployment of innovative products.
Find the Best Scrum, SAFe®, DevOps Course for Your Career
Use our course finder to discover which Scrum, SAFe®, or DevOps certification best suits your career aspirations and expertise.
Try Course Finder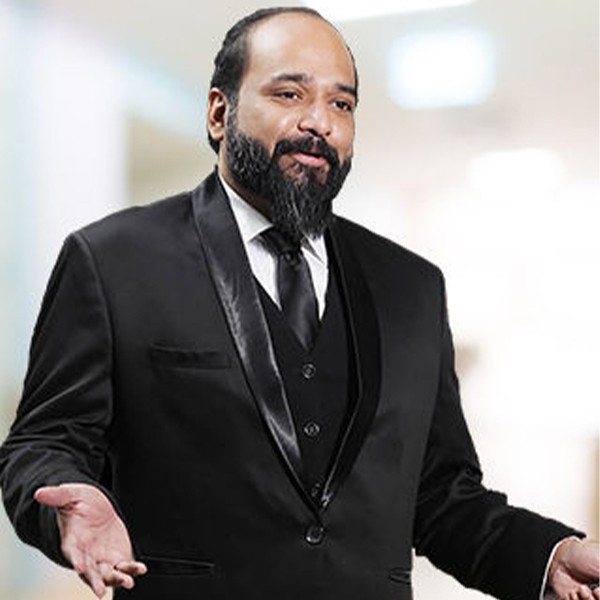
Main Techniques Used in Rapid Prototyping
Several techniques are employed in rapid prototyping, each with its own strengths and applications:
1. Stereolithography (SLA)
Stereolithography utilizes a laser to cure photosensitive resin, constructing objects layer by layer. This technique is commonly applied in fields such as medical, aerospace, and automotive industries. The primary materials used are photosensitive resins, which allow for high precision and an excellent surface finish. However, SLA is limited to smaller objects and can be expensive due to high resin costs.
2. Fused Deposition Modeling (FDM)
Fused Deposition Modeling works by extruding thermoplastic filament layer by layer. It is widely used in product design, education, and consumer applications. This method uses thermoplastic filaments like ABS and PLA, offering versatile materials and ease of use. Despite its advantages, FDM produces lower resolution and surface finish compared to SLA.
3. Selective Laser Sintering (SLS)
Selective Laser Sintering employs a laser to sinter powdered material into solid parts. It finds applications in aerospace, automotive, and medical sectors. SLS typically uses nylon or polyamide powders and produces durable parts without requiring support structures. However, the technique is associated with higher costs, and the surface finish often requires post-processing.
4. Digital Light Processing (DLP)
Digital Light Processing involves using a digital projector to quickly cure resin. It is frequently used in dental and entertainment applications. DLP relies on photosensitive resins, offering fast processing and high resolution. The limitations include a smaller build size and dependence on resin materials.
5. Laminated Object Manufacturing (LOM)
Laminated Object Manufacturing layers adhesive-coated laminates and cuts them into shape. This technique is applied in aerospace and automotive industries, using materials such as paper, plastics, and metal foils. It is known for its low cost and capability for large part production, though it may produce lower accuracy and surface finish.
6. Binder Jetting
Binder Jetting deposits binding agents onto powder layers to form objects. It is used for architectural models and intricate designs, utilizing materials like gypsum, sand, and metals. The advantages include full-color printing and material versatility, but it generally results in lower strength and requires post-processing.
7. Direct Metal Laser Sintering (DMLS)
Direct Metal Laser Sintering uses a laser to sinter metal powders into parts. This technique is applicable in aerospace, automotive, and medical fields, with materials such as stainless steel, titanium, and aluminum alloys. DMLS is noted for its high precision and strength, but it comes with high material and machine costs.
8. Electron Beam Melting (EBM)
Electron Beam Melting employs an electron beam to melt metal powders. It is commonly used in aerospace and medical industries with materials like titanium alloys. EBM produces dense, strong parts with high thermal resistance but requires expensive machines and is limited to specific metals.
9. Selective Laser Melting (SLM)
Selective Laser Melting melts metal powders with a laser to create solid parts. It is used in aerospace, automotive, and medical applications, with materials including stainless steel, aluminum, and titanium alloys. SLM offers the advantage of complex geometries and excellent mechanical properties, although it involves high costs and extensive post-processing.
10. PolyJet Printing
PolyJet Printing jets layers of liquid photopolymer onto a build tray, curing them with UV light. This technique is employed in consumer goods, electronics, and automotive sectors, using various photopolymers. It produces detailed parts with diverse material properties but has limitations in part strength and durability.
11. Injection Molding
Injection Molding involves injecting molten material into molds for high-volume production. It is used in automotive, consumer products, and medical devices, with materials like plastics and some metals. This method is efficient for mass production and offers excellent repeatability, though it incurs high mold creation costs and is not ideal for low volumes.
12. Multi Jet Fusion (MJF)
Multi Jet Fusion applies fusing agents to powder beds and heats them to create parts. It is used in automotive, aerospace, and consumer goods industries, utilizing thermoplastic polymers like Nylon. MJF produces strong parts with fine details and consistent properties but has a limited material range, and the surface finish often requires post-processing.
13. Machining
CNC Machining uses computer-controlled tools to shape solid blocks of material. It is applied in automotive, aerospace, and consumer electronics fields, working with metals, plastics, and composites. CNC Machining is known for its high precision and material versatility, but it involves material wastage and high costs for complex parts.
14. Waterjet Cutting
Waterjet Cutting employs a high-pressure stream of water mixed with abrasives to cut materials. It is used for cutting and shaping metals, glass, and composites. This technique provides clean cuts without heat-affected zones but is limited in cutting thickness and is slower compared to other methods.
15. Vacuum Casting
Vacuum Casting involves pouring liquid material into silicone molds under vacuum conditions. It is commonly applied in consumer electronics, medical devices, and automotive industries.
Conclusion
Rapid prototyping has become an indispensable tool in the modern product development landscape, revolutionizing how products are designed, tested, and brought to market. By enabling swift creation of physical models from digital designs, rapid prototyping significantly accelerates the development process, fosters innovation, and enhances product quality.
The variety of techniques available, from stereolithography and fused deposition modeling to advanced methods like direct metal laser sintering and multi-jet fusion, offers diverse solutions tailored to different needs and industries. Each method comes with its own set of advantages and limitations, making it crucial for teams to choose the right technique based on their specific requirements.